皮带输送机胶带4种撕裂形式及防治措施详述
2022-03-24 06:39
胶带在运行过程中除了正常磨损外,还可能会因其他不利因素,使得胶带撕裂,导致输送机出现故障,影响正常生产,严重时可能导致巨大的经济损失。因此,总结归纳胶带撕裂的常见类型,分析其撕裂原因,采取针对性的防治措施,对矿山安全、高效生产具有重要意义。
1 胶带撕裂的常见形式及原因分析
1、胶带接头撕裂
胶带对接方式主要有两种,一是硫化连接法,二是机械连接法。目前常用的主要是耐磨性相对较好的硫化接头,但其耐压性能较差,在使用过程中常常因矿粉等物料覆盖在钢丝和胶料上而产生腐蚀,直至开胶。
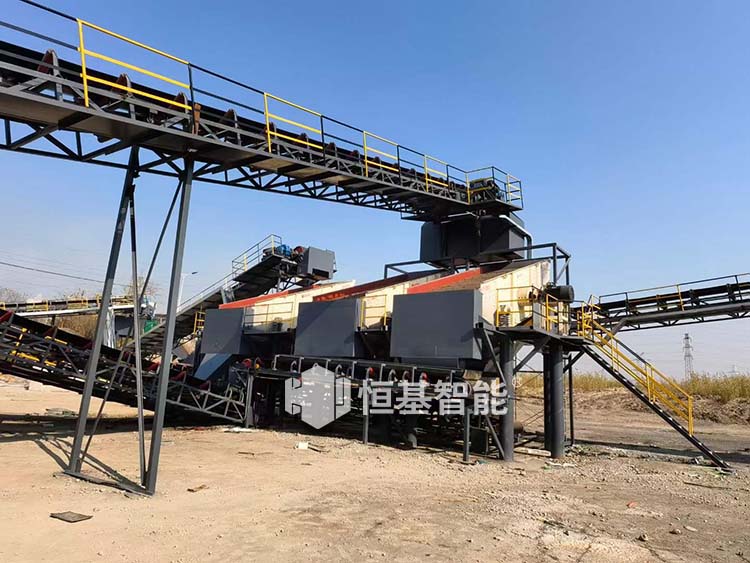
胶带接头也可能因所使用材料不达标,或硫化工艺标准执行不严,出现接口磨损、起皮、开胶、裂纹等现象。如果不及时处理这些问题,物料不断侵蚀以及在滚筒摩擦的作用下,接头部位损伤、劣化速度加快,裂痕不断扩大,胶带强度不断降低,导致接头部位成为整条输送带最薄弱的位置,一旦胶带张紧力突然变大,很容易造成彻底撕裂。
2、胶带纵向撕裂
胶带产生纵向撕裂的概率高于横向撕裂,主要原因有:
(1)物料中如果混入尖锐铁器或未经破碎的铁矿石等,在运行过程中,它们易卡在导料槽下料口及清扫器滚筒等部位,或有脱落的托辊、清扫器等设备部件及尖锐杂物进入滚筒与胶带间造成胶带纵向划伤,导致开裂;
(2)胶带接头及其他部位开胶或局部损伤,如果没有及时修补或更换,随着开裂位置越长,越容易被清扫器、导料槽等卡住,而彻底撕裂。
3、胶带跑偏撕裂
因胶带跑偏导致的撕裂现象最为常见,其根本原因是胶带两侧驱动力大小不一致,产生的摩擦力方向和大小也不相同,或因存在侧向力,使得胶带偏移量达到带宽的 5%以上。胶带过量跑偏后,容易与托辊架、机架等机构产生刮擦、翻边,产生划痕,导致开裂,长时间运行后,开裂部分被卸料器、机架等其他设施不断撕扯,最终彻底断裂。
4.胶带打滑磨裂
胶带正常运行时,理论上其传送速度应与驱动滚筒表面旋转的线速度保持一致,但实际运行时,由于多种因素,很难保证胶带与滚筒转速同步,当带速低于滚筒表面线速度的 95%,或滚筒转动而胶带不转时,就会产生打滑现象。胶带与滚筒之间的摩擦会使胶带的温度不断升高,磨损、劣化加剧、变薄直至开裂。
2.胶带撕裂的防治措施
1、胶带接口横向撕裂控制措施
(1)胶带接口胶接时,控制好硫化温度和硫化压力;
(2)接口处留有合适的长度,过短会直接影响接口的拉力;
(3)严格按国家标准进行胶接,胶接过程中应保持接口部位清洁、干燥
2、胶带纵向撕裂防治措施
(1)在物料源头上控制大块铁矿石、铁件、设备脱落的零部件等进入;
(2)在进料口处加装格筛,出料口加装除铁器等清除大块异物的设施、设备,可防止锐器划裂胶带、卡塞胶带;
(3)根据物料的安息角,导料槽出口顺着胶带输送方向倾斜一定角度,增大导料槽安装弧度,利于排料顺畅,可大大减少大块矿石卡堵现象。
3、胶带跑偏撕裂防治措施
(1)安装滚筒及皮带清扫器,减少粉尘、物料等附着物在滚筒及胶带上的积聚。开机运行前,首先清除滚筒和托辊上的黏连物,然后检查滚筒同轴度,如果滚筒的加工误差偏大,则应重新加工或更换,避免跑偏现象的发生。
(2)调整张紧装置,保持合适的张紧状态。如果运行一段时间胶带出现了永久性变形,或拉紧装置的行程不够,可将胶带截去一小段重新硫化对接。现场实践证明,当拉紧装置两端载荷差距过大时,胶带极易发生跑偏。
(3)安装胶带输送机时,机尾及机头支撑架的安装定位要准确,确保头、尾部滚筒与胶带中心线垂直,机头传动滚筒轴线与机尾滚筒轴线平行,机头与机尾中心线在一条直线上。
(4)安装相应规格的导料槽和导料挡板等缓冲装置,减小物料对胶带的冲击力。
4、胶带打滑磨裂防治措施
(1)合理调整胶带张力,既不能使胶带承受过大张力而降低胶带的使用寿命,也不能使胶带张紧力过小而打滑。对于螺旋和液压拉紧方式,可调整行程增大张紧力,对于重锤拉紧方式,则可增加配重增大张紧力。
(2)加强计量监控,控制物料量,避免过载运行,同时尽量避免重载启动和停机。
(3)当驱动滚筒包胶磨损严重时,应及时重新包胶或更换滚筒,日常巡检中,加强对滚筒的检查,发现问题及时处理。
1 胶带撕裂的常见形式及原因分析
1、胶带接头撕裂
胶带对接方式主要有两种,一是硫化连接法,二是机械连接法。目前常用的主要是耐磨性相对较好的硫化接头,但其耐压性能较差,在使用过程中常常因矿粉等物料覆盖在钢丝和胶料上而产生腐蚀,直至开胶。
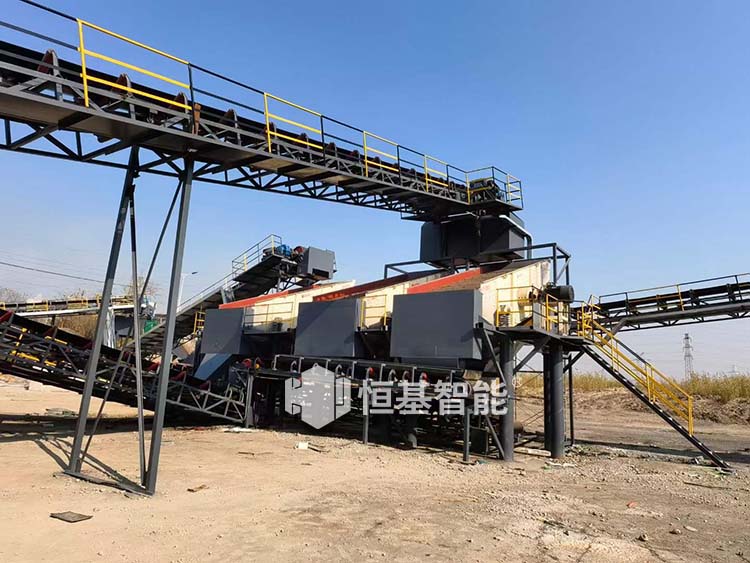
胶带接头也可能因所使用材料不达标,或硫化工艺标准执行不严,出现接口磨损、起皮、开胶、裂纹等现象。如果不及时处理这些问题,物料不断侵蚀以及在滚筒摩擦的作用下,接头部位损伤、劣化速度加快,裂痕不断扩大,胶带强度不断降低,导致接头部位成为整条输送带最薄弱的位置,一旦胶带张紧力突然变大,很容易造成彻底撕裂。
2、胶带纵向撕裂
胶带产生纵向撕裂的概率高于横向撕裂,主要原因有:
(1)物料中如果混入尖锐铁器或未经破碎的铁矿石等,在运行过程中,它们易卡在导料槽下料口及清扫器滚筒等部位,或有脱落的托辊、清扫器等设备部件及尖锐杂物进入滚筒与胶带间造成胶带纵向划伤,导致开裂;
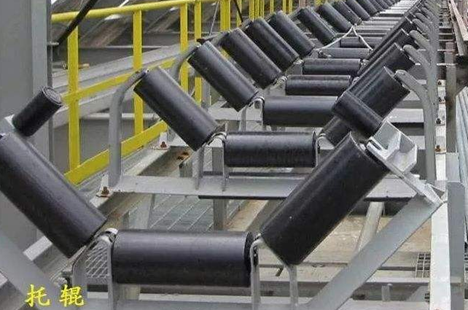
(2)胶带接头及其他部位开胶或局部损伤,如果没有及时修补或更换,随着开裂位置越长,越容易被清扫器、导料槽等卡住,而彻底撕裂。
3、胶带跑偏撕裂
因胶带跑偏导致的撕裂现象最为常见,其根本原因是胶带两侧驱动力大小不一致,产生的摩擦力方向和大小也不相同,或因存在侧向力,使得胶带偏移量达到带宽的 5%以上。胶带过量跑偏后,容易与托辊架、机架等机构产生刮擦、翻边,产生划痕,导致开裂,长时间运行后,开裂部分被卸料器、机架等其他设施不断撕扯,最终彻底断裂。
4.胶带打滑磨裂
胶带正常运行时,理论上其传送速度应与驱动滚筒表面旋转的线速度保持一致,但实际运行时,由于多种因素,很难保证胶带与滚筒转速同步,当带速低于滚筒表面线速度的 95%,或滚筒转动而胶带不转时,就会产生打滑现象。胶带与滚筒之间的摩擦会使胶带的温度不断升高,磨损、劣化加剧、变薄直至开裂。
2.胶带撕裂的防治措施
1、胶带接口横向撕裂控制措施
(1)胶带接口胶接时,控制好硫化温度和硫化压力;
(2)接口处留有合适的长度,过短会直接影响接口的拉力;
(3)严格按国家标准进行胶接,胶接过程中应保持接口部位清洁、干燥
2、胶带纵向撕裂防治措施
(1)在物料源头上控制大块铁矿石、铁件、设备脱落的零部件等进入;
(2)在进料口处加装格筛,出料口加装除铁器等清除大块异物的设施、设备,可防止锐器划裂胶带、卡塞胶带;
(3)根据物料的安息角,导料槽出口顺着胶带输送方向倾斜一定角度,增大导料槽安装弧度,利于排料顺畅,可大大减少大块矿石卡堵现象。
3、胶带跑偏撕裂防治措施
(1)安装滚筒及皮带清扫器,减少粉尘、物料等附着物在滚筒及胶带上的积聚。开机运行前,首先清除滚筒和托辊上的黏连物,然后检查滚筒同轴度,如果滚筒的加工误差偏大,则应重新加工或更换,避免跑偏现象的发生。
(2)调整张紧装置,保持合适的张紧状态。如果运行一段时间胶带出现了永久性变形,或拉紧装置的行程不够,可将胶带截去一小段重新硫化对接。现场实践证明,当拉紧装置两端载荷差距过大时,胶带极易发生跑偏。
(3)安装胶带输送机时,机尾及机头支撑架的安装定位要准确,确保头、尾部滚筒与胶带中心线垂直,机头传动滚筒轴线与机尾滚筒轴线平行,机头与机尾中心线在一条直线上。
(4)安装相应规格的导料槽和导料挡板等缓冲装置,减小物料对胶带的冲击力。
4、胶带打滑磨裂防治措施
(1)合理调整胶带张力,既不能使胶带承受过大张力而降低胶带的使用寿命,也不能使胶带张紧力过小而打滑。对于螺旋和液压拉紧方式,可调整行程增大张紧力,对于重锤拉紧方式,则可增加配重增大张紧力。
(2)加强计量监控,控制物料量,避免过载运行,同时尽量避免重载启动和停机。
(3)当驱动滚筒包胶磨损严重时,应及时重新包胶或更换滚筒,日常巡检中,加强对滚筒的检查,发现问题及时处理。